Heat pump system design process – an expert’s view
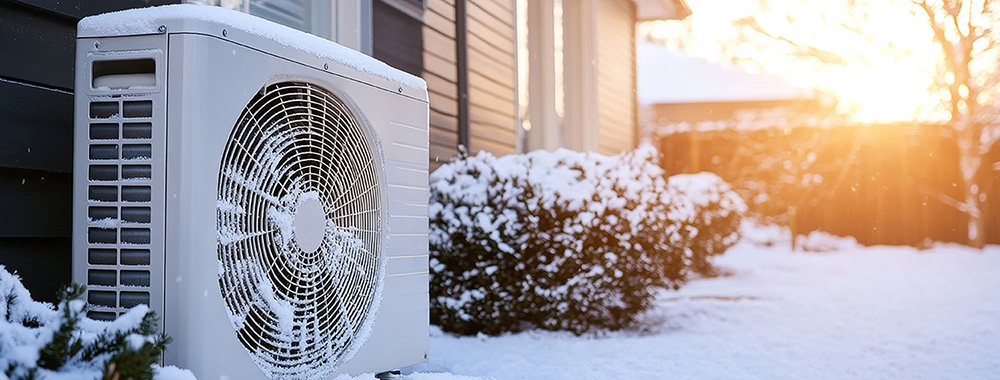
There is a lot of information out there about heat pumps but understanding the basic principles of heating systems in general will help to demystify the transition to low-carbon heating.
Paul Spence, Technical Manager at heatly and experienced heating engineer, shares his time-tested approach and explains why low-temperature design is critical, no matter what the ‘fuel’.
When I design a heating system, there are certain details I need to know before putting pen to paper. You could say my process is tried-and-tested; I’ve done it this way for 40+ years!
The only variable during that time has been the heat generator – I used to do more boilers, now I do more heat pumps. It’s not relevant what the fuel is or how the actual appliance functions, it’s just moving energy from one place to another. Understanding this basic principle of heating system design is a good starting point.
Whenever I design a heat pump system, or any heating system for that matter, I take the following steps:
- Ask the homeowner / user what temperature they want each room to be. The prescribed standard, i.e., 21° living spaces 18° non-living spaces, does not suit everyone. You can design in whatever factors you require. The desired room temperatures will significantly affect the whole house heat loss calculation, so it is the obvious first step.
- Carry out whole house room by room heat loss calculation.
- Decide radiators or under floor heating (UFH).
- If UFH, I send the house plans to the UFH manufacturers’ in-house design service, stating that my max flow temp is 45°, not their preferred 55°. I always get that in writing, it is essential to me. I also stipulate not to design in 200 or 150mm pipe centres, if possible.
- If selecting radiators, I’d set my max flow temp to 45°, just to give me a little tolerance if required.
- Next, I’d size the radiators for each room, based upon the desired room temperature and a 45/40 flow and return. By using a lower flow and return than the heat pump can generate I’m building in a degree of scope. I can always turn it up to achieve more but if I design to the max, this control is removed.
- For a retrofit I also take some detailed measurements of rads and pipes, reverse the formulas to see if they’ll work on my proposed system.
So, by this point I know the:Desired room temperaturesWhole house heat lossHeat emitter selectionPlus, I’ve got my UFH design underway and/or my radiator schedule. - Now I am ready to choose my heat pump.
I already know the load requirement and I calculate the size based on heat loss at -3° in my area. For example, if it’s 10.7kw @ -3, I’m looking for a heat pump that will deliver 10.7kw @ -3° but crucially at 50° flow temp, not 45°. I know at this point I’m factoring in a tolerance for heat loss. Don’t forget, your heat loss calculation is at best an educated guesstimation - you don’t know how good the insulation is or how accurately it’s been applied, or whether the u values are truly reflective of the materials used. It’ll be near; maybe accurate, maybe a bit off. - There won’t be a heat pump exactly 10.7 kW at those parameters, so I select the next size up that matches my requirement, again an extra margin factored in.
- Crucially, I now look at the minimum output, a critical design consideration that is often overlooked.
To maximise efficiency and prevent cycling, I need to understand what the minimum output is likely to be. If the outdoor temperature is, say 15° and I have my desired room temperatures, I can calculate the watts required by reversing the radiator sizing calculation.
If you want more information about how I calculate flow temperatures for the lower end of the curve, you can find detailed instructions the files section of my Facebook Group, Heat Pumps U.K.. - Assume my heat loss at 15° outdoor was 2.7 kW, can the heat pump delivering 10.7 kW or more as necessary modulate down to 2.7 kW? If so, happy days, if not look for a different model, or manufacturer or design in other methods to combat that.
- So, now I know my minimum and maximum range is 10.7kW – 2.7 kW. The heat pump selected may be badged as 16 kW, it means nothing in this context, the 16 kW can only produce 10.7 kW or slightly more as per the manufacturers tables when I actually need the heat.
- Another key question to ask is, is this heat pump suitable for the DNO? Is it on the data base as approved? If yes, happy days.
- Pipe work sizing and circulation pump sizing then come into play. I need to know what the heat pump mass flow rate is, design my pipe circuits to facilitate the flow at max and, importantly, at minimum too. Will the circulation pump be able to supply the pump pressure to overcome the pipe resistances at both minimum and maximum?
The circulation pump flow rate is proportional to the kW output. At lower flow, the pump pressure available is lower but the pipe resistances are reducing with lower flow too. It’s no good if the pressure available is lower than the pipe resistance created at that flow rate. - All the components within the pipe circuit including the heat pump circuit, valves, flow meters, hoses, diverter valves, rad valves, manifolds, radiators etc have a known resistance or pressure loss, they must be included in the overall pipe design.
- Next job, size the hot water cylinder to suit homeowners needs.
Finally, when it comes to controls, I prefer weather compensation open circuit with minimal room interference rather than using TRVs for temperature limiting and room sensing controls feeding back to the heat pump controls.
Essentially, whatever system I am installing, this is the process that I have followed for decades. If its gas fired, I design to flow temperatures of 50/30, which means that all my installations are ‘heat pump friendly’, allowing for a future heat pump upgrade with minimal alterations.
In fact, a boiler at designed at 50/30 has a mean water temperature (MWT) of 40°, so converting that system to heat pump would only require a flow temp of 42.5/37.5 to give the same MWT of 40°. Automatically, a heat pump at 42.5/37.5 is going to have a better co-efficient of performance (COP) than one designed at 55/50 maximum or 50/45.
This is just my way, others will be different. But I know I’ve built in scope to facilitate that bit more output if necessary and run in normal operation at a better COP than the minimum standard design would facilitate.
Want to talk to us?
If you’d like to find out more about Heatly, our team, or our platform, feel free to get in touch.